例:试编写如图4.21所示圆锥螺纹的加工程序。(螺纹导程2mm,升速进刀段=2mm,降速退刀段=1mm,螺纹深度1.0825mm)
……
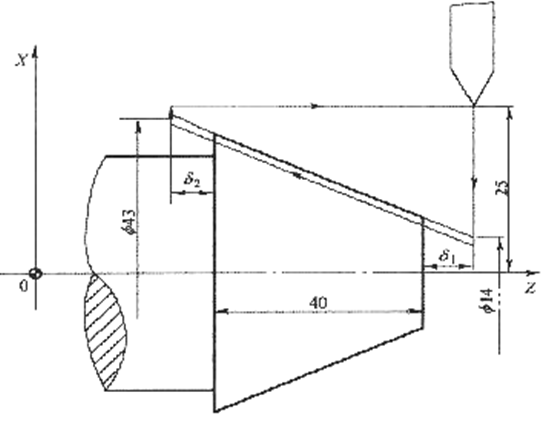
图4.21 圆锥螺纹切削
#p#副标题#e#
◆螺纹切削循环
螺纹切削循环指令把“切入——螺纹切削——退刀——返回”4个动作作为一个循环,用一个程序段来指令,如图4.22所示*
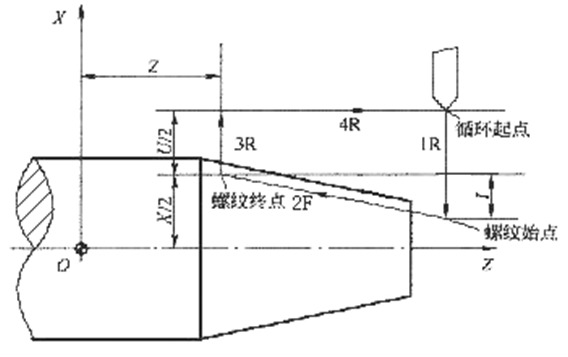
图4.22 螺纹切削循环
指令:G92
程序格式:G92 X(U) Z(W) I F
其中:X(U)、Z(W)——为螺纹切削的终点坐标值;
I——螺纹部分半径之差,即螺纹切削起始点与切削终点的半径差。加工圆柱螺纹时,I=0;加工圆锥螺纹时,当X(W)向切削起始点坐标小于切削终点坐标时,I为负,反之为正。
例:试编写如图4.23所示的圆柱螺纹加工程序。
……
N100 G00 X35 Z104
N110 G92 X29.51 Z56 F1.5
N120 X29.03
N130 X28.54
N140 X28.05
N150 G00 X200 Z200
……
#p#副标题#e#
◆复合螺纹切削循环
复合螺纹切削循环指令可以完成一个螺纹段的全部加工。它的进刀方法有利于改善刀具的切削条件,在编程中应优先考虑应用该指令,如图4.25所示*。
图4.25 复合螺纹切削循环与进刀方法
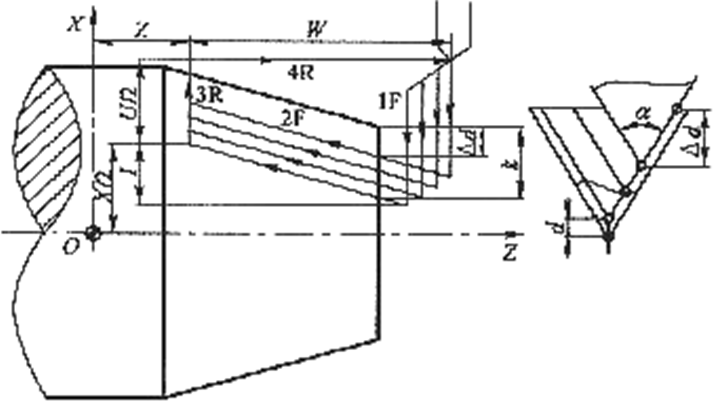
指令:G76
程序格式:G76 P(m)(r)(〆) Q(△dmin)R(d)
G76 X(U)Z(W)R(I)P(k)Q(△d)F(f)
其中:m——精加工重复次数; r——倒角量; △dmin——最小切入量;
d——精加工余量; k——螺牙的高度(半径指定);
△d——第一次切入量(半径指定); f——螺纹导程;
〆——刀尖角,可以选择80°,60°,55°,30°,29°,0°6种,其角度数值用2位数指定;m、r、〆与地址一次指定,如m=2,r=1.2,〆=60°时可写成:P021260;
X(U)、Z(W)——终点坐标;
I——螺纹部分半径之差,即螺纹切削起始点与切削终点的半径差。加工圆柱螺纹时,I=0。加工圆锥螺纹时,当X(U)向切削起始点坐标小于切削终点时,I为负,反之为正。
例:试编写如图4.26所示圆柱螺纹的加工程序,螺距为6mm
……
N100 G76 P021260 Q100 R0.1
N110 G76 X60.64 Z25 P3680 Q1800 F6
……
(8)程序延时
指令:G04
程序格式:G04 P
其中:P——为暂停时间,单位为ms。
该指令可使刀具作短时间的无进给光整加工,常用于车槽、镗平面、锪孔等场合,以提高表面光洁度。采用G04指令使主轴不停,刀具进给短暂停留。
#p#副标题#e#
4.3 典型零件的程序编制
例:图4.27a*中零件Φ85mm不加工,要求编制精加工程序。图4.27b*为刀具布置图及刀具安装尺寸,三把车刀分别用于车外圆、切槽和车螺纹。对刀时,以T01号刀为基准刀,螺纹车刀的刀尖相对T01号刀尖在Z向偏置10mm。加工程序如下:
O001 程序号
N10 G50 X200 Z350 T0101 建立工件坐标系
N20 G97 S650 M03 主轴顺时针旋转,转速650r/min
N30 G00 X41.8 Z292 M08 快进至X=41.8mm,Z=292mm,切削液开
N40 G01 X47.8 Z289 F0.15 工进至X=47.8mm,Z=289mm,倒角
N50 Z230 Z向工进至Z=230mm(精车48.34mm螺纹大径)
N60 X50 X向工进至X=50mm(退刀)
N70 X62 W-60 X向工进至X=62mm,-Z向工进60mm(精车锥面)
N80 Z155 Z向工进至Z=155mm(精车Φ62mm外圆)
N90 X78 X向工进至X=78mm(退刀)
N100 X80 W-1 X向工进至X=80mm,-Z向工进1mm(倒角)
N110 W-19 -Z向工进19mm(精车Φ80mm外圆)
N120 G02 W-60 I63.25 K-30 顺时针圆弧插补,-Z向工进60mm(精车圆弧)
N130 G01 Z65 Z向工进至Z=65mm(精车Φ80mm外圆)
N140 X90 X向工进至X=90mm(退刀)
N150 G00 X200 Z350 T0100 返回起刀点,取消刀具补偿
N160 T0202 换刀,并建立刀具补偿
N170 S320 M03 主轴顺时针旋转,转速320r/min
N180 G00 X51 Z230 快进至X=51mm,Z=230mm
N190 G01 X45 F0.16 X向工进至X=45mm(车Φ45mm槽)
N200 G04 P5 程序延时5毫秒
N210 G00 X51 X向快退至X=51mm(退刀)
N220 X200 Z350 T0200 返回起刀点,取消刀具补偿
N230 T0303 换刀,并建立刀具补偿
N240 S200 M03 主轴顺时针旋转,转速200r/min
N250 G00 X62 Z296 快进至X=62mm,Z=296mm
N260 G92 X47.54 Z231.5 F1.5 螺纹切削循环,螺距1.5mm
N270 X47.02
N280 X46.53
N290 X46.05
N300 G00 X200 Z350 T0300 M09 返回起刀点,取消刀具补偿,同时
关闭切削液
N310 M05 主轴停止
N320 M30 程序结束
例:图4.28所示为。该零件用数控车床加工,要求编制其加工程序。
O002 程序号
N10 G50 X400 Z400 T0101 建立工件坐标系
N20 S300 M03 主轴顺时针旋转,转速300r/min
N30 G00 X118 Z141.5 快进至X=118mm,Z=141.5mm
N40 G01 X82 F0.3 X向工进至X=82mm(粗车端面)
N50 G00 X103 快退至X=103mm
N60 G01 X110.5 Z135 F0.2 工进至X=110.5mm,Z=135mm(粗车短锥面)
N70 Z48 F0.3 Z向工进至Z=48mm(粗车Φ110外圆)
N80 G00 X400 Z400 T0100 返回起刀点,取消刀具补偿
N90 M06 T0303 换刀,并建立刀具补偿
N100 G00 X89.5 Z180 快进至X=89.5mm,Z=180mm
N110 Z145 Z向快进至Z=145mm
N120 G01 Z61.5 F0.3 Z向工进至Z=61.5mm(粗车Φ90mm内孔)
N130 X79.5 X向工进至X=79.5mm(粗车内孔阶梯面)
N140 Z-5 Z向工进至Z=-5mm(粗车Φ80mm孔)
N150 G00 X75 X向快退至X=75mm
N160 Z180 Z向快退至Z=180mm
N170 G00 X400 Z400 T0300 返回起刀点,取消刀具补偿
N180 M06 T0505 换刀,并建立刀具补偿
N190 S600 M03 主轴顺时针旋转,转速600r/min
N200 G00 X85 Z145 快进至X=85mm,Z=145mm
N210 G01 Z141 F0.5 Z向工进至Z=141mm
N220 X102 F0.2 X向工进至X=102mm(精车端面)
N230 U8 W-6.93 X向工进至U=8mm,-Z向工进至W=-6.93mm
(精车短锥面)
N240 Z48 F0.08 Z向工进至Z=48mm(精车Φ110mm外圆)
N250 G00 X112 X向快退至X=112mm
N260 X400 Z400 T0500 返回起刀点,取消刀具补偿
N270 M06 T0707 换刀,并建立刀具补偿
N280 S200 M03 主轴顺时针旋转,转速200r/min
N290 G00 X85 Z180 快进至X=85mm,Z=180mm
N300 Z133 T0707 Z向快进至Z=133mm,刀具补偿
N310 G01 X93.8 F0.2 X向工进至X=93.8mm(车Φ93.8mm槽)
N320 G00 X85 X向快退至X=85mm
N330 Z180 Z向快退至Z=180mm
N340 X400 Z400 T0700 返回起刀点,取消刀具补偿
N350 M06 T0909 换刀,并建立刀具补偿
N360 S600 M03 主轴顺时针旋转,转速600r/min
N370 G00 X94 Z180 快进至X=94mm,Z=180mm
N380 Z142 Z向快进至Z=142mm
N390 G01 X90 Z140 F0.2 工进至X=90mm,Z=140mm(内孔倒角)
N400 Z61 Z向工进至Z=61mm(精车Φ90mm内孔)
N410 X80 X向工进至X=80mm(精车内孔阶梯面)
N420 Z-5 Z向工进至Z=-5mm(精车Φ80mm内孔)
N430 G00 X75 X向快退至X=75mm
N440 Z180 Z向快退至Z=180mm
N450 X400 Z400 T0900 返回起刀点,取消刀具补偿
N460 M06 T1111 换刀,并建立刀具补偿
N470 S240 M03 主轴顺时针旋转,转速240r/min
N480 G00 X115 Z71 快进至X=115mm,Z=71mm
N490 G01 X105 F0.1 X向工进至X=105mm,刀具补偿
(车4.1mmX2.5mm槽)
N500 G00 X115 X向退回至X=115mm
N510 X400 Z400 T1100 M09 返回起刀点,取消刀偿,关闭切削液
N520 M05 主轴停止
N530 M30 程序结束
#p#副标题#e#
4.4 思考与练习题
1.如题图4.1*、4.2*、4.3*所示的零件,编写数控车削加工程序。
2.如题图4.4*、4.5*、4.6*、4.7*所示的零件,试分别编写数控车削加工程序,要求如下:
(1)确定加工方案,并画出走刀路线;
(2)选择合适的刀具;
(3)计算刀尖轨迹坐标值。